Faktensheet
- Abstimmung aller Lagerprozesse mit Intervall-Logik
- Auf Anforderungen abgestimmte Lagerplatzzuordnung
- Gesteigerte Effizienz durch Prozessoptimierungen
- Optimierte Ressourcenplanung in Anbhängigkeit von Nachfrage

Optimiertes Lagermanagement im Fulfillment Center
Die weltweite Drittlogistikbranche wird bis 2030 voraussichtlich mehr als 2 Billionen USD erreichen - Logistikdienstleistern ging es noch nie besser. Jedoch waren auch die Anforderungen noch nie so komplex wie heute. Ständig steigende Kundenerwartungen, verflochtene Lieferketten und der harte Wettbewerb verlangen den Anbietern Höchstleistungen ab.
Das Herzstück eines jeden Logistikdienstleisters ist das Fulfillment Center. Es gibt sie in allen Formen und Größen, von lokalen Hubs, die ein Dutzend Kunden und ein paar Tausend Artikel abwickeln, bis hin zum Amazon Fulfillment Center, das über vierzehn Fußballfelder groß ist.
Auf den ersten Blick sind die Aufgaben des Fulfillment Centers einfach: Lagern, Kommissionieren und Bereitstellen für die Auslieferung. Wenn man dies jedoch auf Millionen von Einzelartikeln hochrechnet, wird es schnell komplex. Zudem haben ineffiziente Lagerprozesse schwerwiegende Konsequenzen: beeinträchtigte Rentabilität; Vertragsstrafen auf Grund verpasster SLAs und nicht zuletzt unzufriedene Kunden. Kurz gesagt, ein schlecht verwaltetes Fulfillment Center wird kaum wachsen und oft auch nicht überleben.
Unser Kunde stand genau vor diesen Problemen. Ihm fehlte die Reife, um das aktuelle Volumen und die Komplexität zu bewältigen. Die Kommissionierung dauerte zu lange, Lieferungen gingen nicht rechtzeitig vom Hof und die Fehlerquote hatte längst ein inakzeptables Niveau erreicht. An dieser Stelle wurde OCM beauftragt, die Lagerprozesse & das Lagermanagement wieder auf Kurs zu bringen.
Nachfolgend erläutern wir, wie wir die Performance des Fulfillment Centers optimierten, indem wir beispielsweise eine vierfach bessere Lieferpünktlichkeit erreichten, und so unseren Kunden vor der existenziellen Bedrohung bewahrten.
Hintergrund: Wachstum übertrifft Reifegrad des Fulfillment Centers
Unser Kunde war Teil eines größeren Logistikkonzerns und operierte als spezialisierter Fulfillment-Anbieter ein 20.000 m2 großes Lager mit über 66.000 einzelnen Lagerplätzen. Hierin wurde eine Reihe von Dienstleistungen für Online-Shops angeboten, wie Wareneingang und -lagerung, Kommissionierung, Verpackung und Versand an B2B- und B2C-Kunden.
Wie die meisten Logistikdienstleister hatte auch unser Kunde während der Corona-Pandemie einen starken Anstieg des Geschäftsvolumens erlebt und verfügte über zu wenig Zeit und Ressourcen, um das neue Volumen auf eine zukunftsorientierte und strategische Weise zu integrieren. Die Altsysteme waren längst überholt und alte Arbeitsweisen wurden nicht in Frage gestellt. Die Mitarbeiter waren überlastet und demoralisiert.
Das größte Problem hierbei war der große Backlog auf Grund von Werbeaktionen und dem Weihnachtsgeschäft. Der Anteil der verspäteten Lieferungen war höher als der Anteil der Pünktlichen. Kunden waren unzufrieden und drohten, den Anbieter zu wechseln. Um die Kunden bei der Stange zu halten und das Geschäft am Laufen zu halten, wurden die Preise für die Logistikdienstleistung schon seit einiger Zeit nicht mehr erhöht. So war der Betrieb für unseren Kunden unrentabel. Alle hatten das Nachsehen.
Da das Überleben des Unternehmens auf dem Spiel stand, musste unser Kunde seine Leistung verbessern - und zwar schnell.
Informationserfassung und Analyse des Lagermanagements
In einem ersten Schritt führten wir eine ausführliche Bestandsaufnahme vor Ort durch. Dazu gehörten Workshops mit Mitarbeitern, unter anderem aus den Bereichen IT, Kundendienst, Vertrieb, Finanzen und dem Lager selbst. Außerdem nahmen wir eine mehrtägige Bewertung der Lagerprozesse in Form einer Zeit- und Bewegungsstudie vor.
Diese beiden Aktivitäten ermöglichten es uns, einen anekdotenhaften Bericht über die Herausforderungen zu erstellen, mit denen das Fulfillment-Center und seine Mitarbeiter konfrontiert waren. Gleichzeitig konnten wir so auch die Lagerprozesse abbilden und unsere eigene Bewertung des Lagermanagements vornehmen.
Parallel dazu führten wir eine umfassende Datenerhebung durch. Zunächst prüften wir Kundenverträge, Gewinn- und Verlustrechnungen und die aktuellen Preise. So konnten wir uns ein Bild von der Rentabilität des aktuellen Geschäftsmodells sowie durch Kundenvereinbarungen gesetzte Anforderungen machen.
Vor allem aber haben wir digitale Lagerlayouts und standardisierte Daten aus dem Lagerverwaltungssystem abgefragt, darunter Rechnungen, anfallende Mengen im Lagermanagement, Dauern von Lagerprozessen und weitere anonymisierte operative Daten. Auf dieser Grundlage konnten wir ein 'Multi-Layer Path Model' erstellen. Dieses Modell berechnete die Entfernung von einem beliebigen Punkt zu einem anderen im Lager, indem es diese in Entfernungen zwischen Bereichen, Reihen und Regalen unterteilte und addierte. Auf diese Weise konnten wir die Effizienz des derzeitigen Lagerlayouts bestimmen und im Anschluss den Vergleich zu einer Reihe von verbesserten Szenarien quantitativ nachvollziehen.
Ineffizienzen in Lagerlayout und Lagerprozessen des Fulfillment Centers
Die Ergebnisse unserer ersten Untersuchungen zum Lagermanagement waren wie folgt:
Aufgrund des hohen Geschäftsaufkommens und der schrittweisen Vergrößerung der Lagerfläche konnte ein einziger Kunde auf mehrere Bereiche im Lager verteilt sein. Dies bedeutete, dass die Kommissionierer für einen einzigen Auftrag auch mehrere Lagerbereiche aufsuchen mussten. Darüber hinaus wurden Kunden die Lagerbereiche nicht nach der Häufigkeit der Zugriffe zugeteilt. Das heißt, ein Kunde mit wenigen Aufträgen war beispielsweise nahe an der Packstraße und dem Zugang zum Nachschublager platziert, wobei ein hochfrequentierter Kunde weiter entfernt angeordnet wurde und dadurch schlecht an die Lagerinfrastruktur angebunden war. So verlängerten sich die Kommissionierläufe und Ressourcen konnten nicht effizient genutzt werden.
Wir ermittelten, dass es 23 % länger dauerte, aus einem oberen oder unteren Regalfach zu kommissionieren als aus einem mittleren. Im Lagermanagement wurde die vertikale Position eines Artikels bei der Organisation eines Kundenbereichs jedoch nicht berücksichtigt. Schnelldrehende Artikel wurden nur zufällig auf der mittleren Ebene platziert, viele landeten auf den schwer erreichbaren Regalfebenen. Ebenso wurden Schnelldreher nicht am Anfang der Reihen platziert, wo sie schneller zugänglich waren. Stattdessen musste jede Reihe bis zum Ende durchlaufen werden - eine weitere Ineffizienz.
Die Umlagerungseinstellungen des Lagerverwaltungssystems waren nicht optimiert oder gar in Frage gestellt worden. Infolgedessen machte die Software oft falsche oder unsinnige Vorschläge für die Einlagerung von Nachschub im Kommissionierlager. Lagermitarbeiter überschrieben daher die Vorschläge der Software und lagerten in ein anderes Fach um. Da diese Entscheidungen auf der Grundlage begrenzter Informationen und einem „Bauchgefühl“ getroffen wurden, resultierten weitere Ineffizienzen. So nutzten Mitarbeiter beispielsweise häufig neue, nahegelegene Fächer, anstatt alte Fächer aufzufüllen. Die Folge war ein ineffizientes Warenlayout - in einigen Fällen gab es bis zu 10 verschiedene Fächer (mit Restmengen) für einen einzigen Artikel.
Wenn der Bestand eines Artikels im Kommissionierlager unter einen Karton fiel, wurde der Bestand standardmäßig mit drei Kartons aus dem Hochregallager aufgefüllt. Für Artikel mit geringer Umschlagshäufigkeit waren drei Kisten zu viel, was zu Platzverschwendung führte. Und für Artikel mit hoher Umschlagshäufigkeit war die auslösende Menge von einem Karton zu niedrig, sodass der Nachschub zu spät erfolgte und temporäre Fehlbestände mit sich brachte.
Die Teams und entsprechenden Lagerprozesse im gesamten Fulfillment Center waren nicht aufeinander abgestimmt und agierten unabhängig voneinander. Insbesondere die Kommunikation zwischen dem Nachschublager und dem Kommissionierlager war ineffektiv; Auftragsspitzen und die gegenseitigen Abhängigkeiten der Lagerprozesse wurden nicht berücksichtigt. Während die Kommissionierer beispielsweise nach den SLAs der Kunden arbeiteten, war dies im Nachschublager nicht der Fall. Infolgedessen musste die Kommissionierung zu lange auf den Nachschub warten, und es kam zu Verzögerungen im Prozess, bis hin zur verspäteten Auslieferung der Sendungen.
Die Kommissionierläufe selbst waren schlecht geplant und basierten auf Standard-Softwareeinstellungen und einem "Bauchgefühl". Kommissionierer begannen ihre Läufe, ohne zu warten, bis sich genügend zu bearbeitende Aufträge angesammelt hatten. So war zu keinem Moment eine ausreichende Menge an Aufträgen ausstehend und die Software konnte keine effizienten Multi-Order-Kommissionierläufe bilden. Die Kommissionierer kehrten mit halb gefüllten Wagen zurück und brachen zügig zu einem weiteren ineffizienten Lauf auf. Dies führte zu zusätzlichen Kilometern in den Beinen und insgesamt weniger abgearbeiteten Aufträgen.
Wie bei allen Logistikvorgängen gab es auch in unserem Fulfillment Center Nachfragespitzen und -tiefs. Die Spitzen traten sowohl kurzfristig, z. B. in den Stunden vor dem Versandschluss, als auch saisonal auf, z. B. in der Weihnachtszeit. Jedoch wurde die Personaleinsatzplanung als Teil des Lagermanagements nicht an den bekannten Spitzen ausgerichtet. Alle Mitarbeiter starteten zu Tagesbeginn, wenn es oft noch weniger zu tun gab, und nur die gleiche Anzahl Mitarbeiter war zum geschäftigen Tagesende verfügbar. Aus Gewohnheit hielten die Mitarbeiter auch in der Hochsaison an ihren starren Arbeitszeiten fest und buchten teilweise ihren Jahresurlaub zur gleichen Zeit. So war das Lager vor allem zu Nachfragepeaks heillos unterbesetzt. Der Backlog stieg und konnte auch nicht abgebaut werden.
Optimierung des Lagermanagements
Nachdem wir die Ergebnisse zusammengetragen hatten, leiteten wir diverse Maßnahmen ab, um das Lagermanagement im Fulfillment Center zu optimieren, die Leistung zu verbessern und letztendlich die Kunden zu binden.
Optimierung der Bereichszuordnung:
Mithilfe unseres Multi-Layer-Path-Modells konnten wir eine Kosten-Nutzen-Analyse verschiedener Lagerlayouts durchführen. Dies ermöglichte uns, die Verteilung der Kundenbereiche auf fundierte Weise zu gestalten und zu optimieren. Wir konsolidierten Kunden in einzelne Bereiche oder in mehrere angrenzende Bereiche, sodass Lagermitarbeiter nicht mehr das ganze Fulfillment Center durchqueren mussten, um Aufträge eines einzelnen Kunden zu bearbeiten. In diesem Zug platzierten wir außerdem wichtige, hochfrequentierte Kunden nahe der Packstraße und den Kommissionierzugängen, was die Wegezeiten für diese Kunden signifikant reduzierte.
Verbesserte Lagerplatzzuordnung:
Wir kategorisierten alle Produkte als Langsam-, Mittel- oder Schnelldreher. Schnelldrehende Artikel wurden von nun an von der Software nur in den mittleren Regalen platziert, wo die Kommissionierung am schnellsten ist. Da die Kommissionierung von Lagerplätzen in der obersten und untersten Ebene deutlich länger dauert, wurden diese hingegen nur langsam drehenden Artikeln zugeordnet. Auch die Größe der Artikel wurde zu einem entscheidenden Faktor für die Zuordnung der Lagerplätze: Kleine Artikel wie Kopfhörer und Textilien wurden nicht mehr in große Fächer gelegt, deren Platz sie nicht ausfüllen. Darüber hinaus wurden Artikel, die häufig zusammen bestellt wurden, in nahegelegene Fächer platziert, um die Kommissionierwege zu reduzieren.
Verbesserte Wiedereinlagerungsprozesse:
Wir entwickelten eine neue Lagerplatzstrategie und implementierten die in der Abbildung dargestellte Logik im Lagerverwaltungssystem. So wurden nur neue Fächer eröffnet, wenn zwingend notwendig, sonst wurde in bestehende Lagerplätze zugelagert. Mit neuem Vertrauen in die Software, konnten wir außerdem das Überschreiben vorgeschlagener Fächer abstellen und Umlagerungsmitarbeiter verpflichten, die Empfehlungen zu befolgen. Des Weiteren passten wir die Software-Einstellungen so an, dass Kommissionierer Artikel vorrangig aus den leersten Fächern entnehmen. So schufen wir ein "selbstreinigendes" System, das halbgefüllte Fächer bevorzugt entleert und Lagerplatz wieder schnell zur Verfügung stellt.
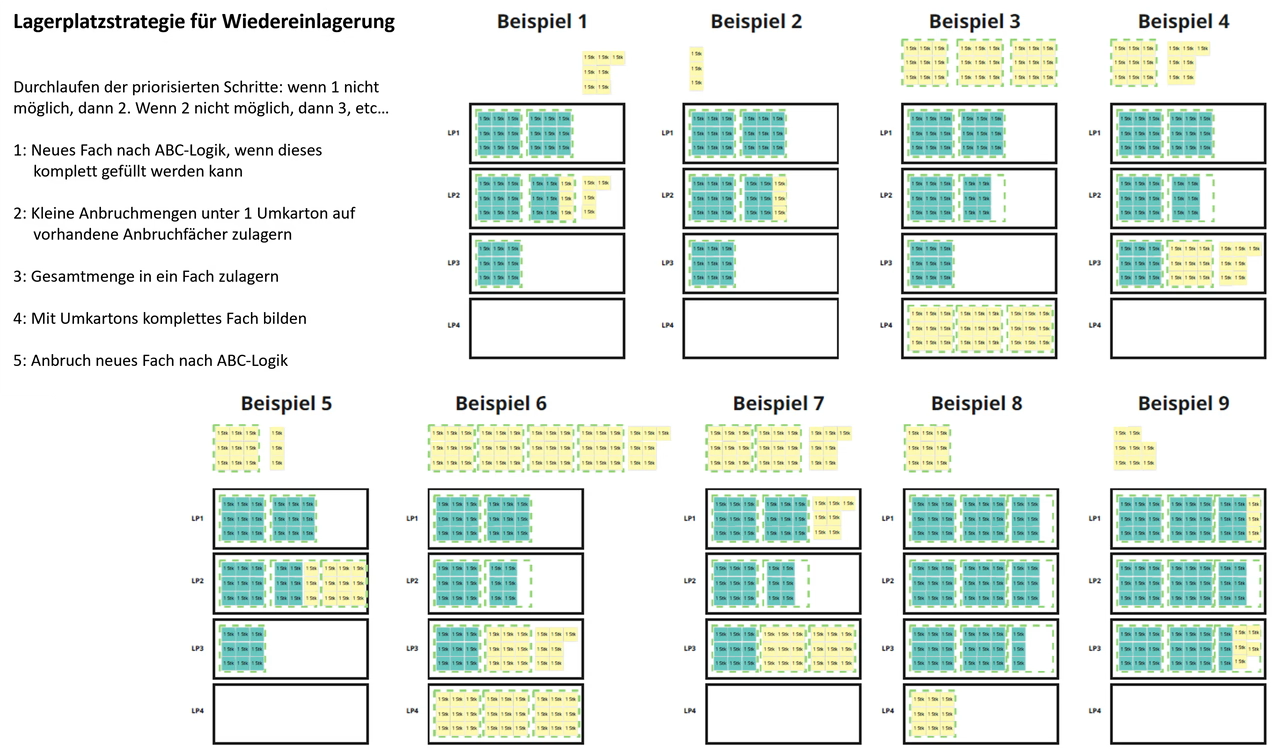
Verbesserte Nachschubparameter:
Auf der Grundlage historischer Daten berechneten wir zwei Dinge: den Nachbestellpunkt je Artikel und die Nachschubmenge für jeden Artikel. Dadurch wurden die Fächer für Artikel mit geringer Umschlagshäufigkeit nicht unnötig überfüllt, während für Schnelldreher nun genügend Zeit zur Verfügung stand, um den Bestand aufzufüllen, bevor es zu einem Stockout kam. Außerdem wurden für schnelldrehende Artikel mehr als bisher drei Kartons umgelagert, sodass maximal einmal am Tag Nachschub benötigt wurde.
Einführung von getakteten Kommissionierläufen:
Während früher Lagerprozesse kontinuierlich und nach "Bauchgefühl" durchgeführt wurden, führten wir ein Takt-System ein, bei dem bestimmte Lagerprozesse je nach Bedarf alle 1-5 Stunden angestoßen wurden. Mit der entsprechenden Parametrisierung im System häuften sich so die Aufträge an und es konnten effizientere Läufe gebildet werden. In der Kommissionierung führte dies zu vollen Wagen und insgesamt kürzeren Kommissionierwegen.
Anpassung der Wagen:
Um das volle Potenzial der neuen getakteten Kommissionierläufe zu nutzen und die Auftragsmerkmale der Kunden optimal abbilden zu können, bauten wir außerdem einige der Kommissionierwagen von 9 auf 12 Fächer um. Der zweitgrößte Kunde beispielsweise war ein B2C-Unternehmen mit kleineren Aufträgen. Daher konnten mehr Aufträge in einem Durchgang kommissioniert werden, was die Effizienz eines Kommissionierlaufs signifikant verbesserte.
Optimierung der Hardware:
Ein auf den ersten Blick trivialer Punkt, der in der Praxis jedoch zu endloser Frustration und zu Verzögerungen führte, war der Betrieb von überlasteten und langsamen Geräten, wie Drucker und Scanner. Aktualisierungen der Software und der APIs sorgten für einen effizienteren Betrieb der Hardware und verbesserten die Druckzeiten für Etiketten und Dokumente.
Intervall-Logik zur Integration von Lagerprozessen:
Nach der detaillierten Prozessaufnahme konnten wir alle Punkte auf dem kritischen Pfad zum Versand einer Bestellung bestimmen. Dazu gehörten bestimmte Zeitpunkte, z. B. wann die Aufträge in das System geladen wurden, wann der Nachschub ausgelöst wurde und wann die Kommissionierläufe gebildet und ausgeführt wurden. Ausgehend von den vertraglichen SLAs und den Abholzeiten der Spediteure, entwickelten wir eine neue Logik, die in einer „Rückwärts-Rechnung“ alle genannten Prozesse und Zeitpunkte koordinierte. Dies führte insgesamt zu kürzeren Wartezeiten und höherer Effizienz. Eine wichtige Voraussetzung für diese gesamtheitliche Intervall-Logik über alle Lagerprozesse hinweg war die zuvor genannte Umstellung auf getaktete Kommissionierläufe. Für das Lagermanagement ermöglichte dies eine punktuelle Ausrichtung, Berechnung und Planung anstelle von kontinuierlichen und oft ungenauen (Neu-)Berechnungen.
Optimierte Ressourcenplanung:
Wir führten neue Arbeitspläne ein, um die Spitzen und Tiefpunkte im Tagesverlauf zu berücksichtigen. So wurden die Anfangszeiten der Mitarbeiter je nach Auftragslast gestaffelt, so dass nicht alle Mitarbeiter zur gleichen Zeit starteten und mehr Mitarbeiter vor Abholung durch die Spediteure im Einsatz waren. Gleitzeit und Zeitkonten ermöglichten es dem Kunden außerdem, saisonale Arbeitsspitzen mit internem Personal zu bewältigen. Darüber hinaus sorgte eine neue Urlaubsregelung - z. B. ein maximaler Anteil von Mitarbeitern, die sich vor Weihnachten im Urlaub befanden - dafür, dass das Fulfillment Center nicht mehr mit Notlagen auf Grund zu wenig Personals konfrontiert war.
Ergebnisse des optimierten Lagermanagements
Die Umsetzung der oben genannten Maßnahmen führte zu erheblichen Effizienzsteigerungen im Lagermanagement, deren größte Erfolge im Folgenden dargestellt werden.
-
Das neue Lagerlayout führte zu einer Reduzierung der Kommissionierzeiten um 17%
-
Die Einführung von Intervallen für den Nachschub führte zu einer Verringerung der Fehlbestände im Kommissionierlager um 20%
-
Zu Beginn des Projekts lag der Prozentsatz der pünktlichen Auftragspositionen bei nur 15 %. Am Ende des Projekts hatte sich der Anteil der pünktlichen Positionen auf 60 % vervierfacht
-
Die Zahl der mit mehr als 3 Tagen Verspätung gelieferten Artikel sank von 55 % auf 2,5 %.
Diese Effizienzsteigerungen führten unter anderem zu jährlichen Einsparungen in Höhe von über 400k Euro, die sich wie folgt aufteilen:
-
Durch die Optimierung der Lagerlayouts (z. B. Optimierung des Kundenbereichs) erzielten wir jährliche Einsparungen in Höhe von 120k EUR.
-
Durch Verbesserungen der Prozesseffizienz (z. B. Getaktete Kommissionierläufe, Angepasste Kommissionierwagen und Hardwareverbesserungen) konnten wir jährliche Einsparungen in Höhe von 127k EUR erzielen.
-
Durch Verbesserungen bei der Fachzuteilung und der Intervall-Logik für den Warennachschub konnten wir jährliche Einsparungen in Höhe von 190k EUR erzielen.
Darüber hinaus entwickelten wir weitere Maßnahmen für den Kunden, die auf eines seiner Hauptprobleme abzielen: die Preisgestaltung.
Mit der neuen verbesserten Leistung konnte der Kunde seinen Ruf wiederherstellen und die Preise wieder auf den Industriestandard anheben. Aber es ging nicht nur darum, mehr Geld zu verlangen.
Erstens musste unser Kunde glaubhaft nachweisen, dass sich seine Leistung verbessert hatte. Wir empfahlen eine Reihe neuer Datenmanagementmaßnahmen und verbesserter KPIs, um die Einhaltung und sogar das Übertreffen der vertraglichen SLAs nachzuweisen.
Zweitens empfahlen wir eine datengesteuerte Preisverhandlung. Anstatt mit dem Rücken zur Wand in die Verhandlungen zu gehen und sich den Forderungen des Kunden zu beugen, konnte man so mit evidenzbasierten Behauptungen in die Verhandlungen gehen und seine Preise rechtfertigen.
Wir schätzten die daraus resultierende jährliche Umsatzsteigerung auf über 1 Million EUR.
Optimierung des Lagermanagements: Abschließende Überlegungen
Ineffiziente Lagerplatzzuweisung, überlange Kommissionierwege, verpasste Liefertermine: Unser Kunde betrieb ein suboptimales Fulfillment Center und sah sich mit drastischen Konsequenzen konfrontiert.
Durch eine detaillierte Aufnahme der Lagerprozesse und Datenanalyse identifizierte OCM die Ursachen der Probleme im Lagermanagement und implementierte praktische Lösungen. Dies führte zu Effizienzsteigerungen und erheblichen finanziellen Einsparungen.
OCM bietet eine Reihe von Beratungsdienstleistungen in der Logistikoptimierung an, darunter Lagerplanung, Lageroptimierung und mehr. Wenn Ihr Unternehmen mit ähnlichen Schwierigkeiten konfrontiert ist und Sie wissen möchten, wie wir Ihnen helfen können, zögern Sie bitte nicht, uns zu kontaktieren.

Module Logistik Optimierung & Supply Chain Consulting
Potentialanalyse Logistik & SCM
- Identifikation von Potentialen
- Maßnahmenplan zur Realisierung
Transport Partner Management
- Partnerstrategie und Professionalisierung
- Ressourcensicherung und Schulungskonzept
Ausschreibung Transport
- Professionelle Ausschreibung von Transportdienstleistungen unter Wettbewerb
- Kostenreduzierung Transport
Ausschreibung Fracht- & Logistik
- Kompetitive Bepreisung des exakten Routenprofils
- Qualitäts- und Leistungssicherung
Lageroptimierung & Lagerlogistik
- Kostenoptimierung Warenlager
- Bedarfsgerechtes effizientes Lagerkonzept
Logistik Kooperation
- Transportkosten reduzieren durch Synergie
- Faires und stabiles Kooperationsmodell finden
Tourenplanung & Wegeoptimierung
- Kilometer und Routenreduktion
- Ressourceneinsparung
Supply Chain Netzwerk Design
- Optimierte Kosten je Servicelevel
- Reduzierte Kapitalbindung
Bestands- & Bestellmengen Management
- Bedarfsgerechte Bestand- und Bestellmengenprozesse
- Reduktion Lagerhaltungskosten
Fuhrparkoptimierung
- Optimiertes Fuhrparkkonzept
- Kostenoptimierung & Effizienzsteigerung
Supply Chain & Logistik Strategie
- Ausrichtung der Supply Chain nach Qualität, Verfügbarkeit und Kosten
Digitales Logistikmanagement & Reporting
- Ressourceneffizient
- Aussagekräftige Analysen fundierte Entscheidungen
Interim Manager Logistik & Supply Chain
- Schnelle Hilfe: Kandidaten innerhalb von 48h
- Abgleich von Anforderung und Eignung vom Logistikexperten
- Vom Disponenten bis Logistikleiter