- Supply Chain Strategie
- Supply Chain Netzwerk
- Lagerbestand & Optimale Bestellmenge
- Routenoptimierung
- Ausschreibung Fracht & Distributionslogistik
- Lageroptimierung & Lagerlogistik
- Transportausschreibung
- Digitale Supply Chain

Lageroptimierung und Lagerlogistik: Wie Ihr Lager zum Unternehmenserfolg beiträgt
Durch Lageroptimierung und die Gestaltung effizienter Lagerlogistik werden Roh- und Hilfsstoffe, Halbfertig- und Fertigprodukte kostenoptimal vorgehalten, kommissioniert, versendet, und so der Supply Chain im Bedarfsfall schnell zugeführt. Die Zunahme von Just-in-time Strategien, steigender Variantenvielfalt, kürzeren Lieferzeiten und erhöhtem Fokus auf das Working Capital erhöhen die zu bewältigen Aufgaben ebenso wie den Kostendruck auf die Lager. Der Wettbewerbsfaktor Lager ist längst angekommen im Kampf der Supply Chains. Vor diesem Hintergrund ergeben sich Fragestellungen wie:
- Der Wertbeitrag einer Lageroptimierung wird oft unterschätzt – zurecht?
- Eignet sich das Lager hinsichtlich Ausrichtung, Struktur und Dimensionierung?
- Wie kann eine Optimierung der Lagerlogistik und Lagerplatzzuordnung Lagerkosten senken und die Lagerperformance steigern?
- Welchen Einfluss haben Kommissioniertechniken, Verpackungssysteme und Beladungsplanung?
- Welchen Beitrag leistet die Digitalisierung durch ein Warehouse Management System?
Im Folgenden beleuchten wir die relevantesten Fragenstellungen, diskutieren Herausforderungen und Lösungsansätze und geben einen Ausblick wie Supply Chain Entscheider mit Lageroptimierung einen entscheidenden Wertbeitrag zum Unternehmenserfolg erbringen können.
Der Wertbeitrag einer Lageroptimierung kann enorm sein – warum eigentlich?
Lagerverantwortliche und Supply Chain Entscheider wissen normalerweise um die Rolle und den Beitrag den ein gut aufgestelltes Lager für eine Supply Chain und den Wertbeitrag innerhalb des Unternehmens leisten kann. Um diesen Beitrag kontinuierlich zu erbringen, ist jedoch eine regelmäßige und vor allem strategische Weiterentwicklung und Anpassung des Lagers notwendig.
Ziel der Lageroptimierung ist es die Lagerkosten, die Lagerlogistik und das Working Capital zu senken und gleichzeitig die Performance des Lagers zu maximieren. Die Unterschiede hinsichtlich Lagerhaltungskosten, Working Capital und Performance eines optimierten Lagers gegenüber einem seit langer Zeit bestehenden und über die Zeit kaum strategisch betrachteten Lagers können jedoch immens sein. Die jährlichen Gesamtkosten eines Lagers durch Miete, Abschreibungen und Personal zählen oft zu den größten unbeachteten Kostenblöcken im Unternehmen. Ein häufiger Grund hierfür ist eine fehlende Überprüfung - Potentiale werden nicht erkannt oder Veränderungen von vorneherein als zu komplex eingestuft.
Darüber hinaus bleiben Lageroptimierungen oftmals aus, weil den Lagerverantwortlichen neben dem operativen Geschäft oftmals schlichtweg die Zeit fehlt. Beispielsweise sind die strategische Überprüfung des Einflusses der Lagerstruktur auf das Working Capital oder der Personalkosten durch ineffizienten Materialfluss zeitintensive und zudem analytisch anspruchsvolle Bewertungen, die ebenfalls Kenntnis der neusten Entwicklungen am Markt erfordern.
Um neue Entwicklungen und Betrachtungswinkel mit in die Überlegungen einfließen zu lassen sowie dem Risiko einer sich historisch eingestellten „Betriebsblindheit“ entgegenzuwirken, sollten Sie prüfen ob Ihre bestehenden Lager in folgenden 4 Punkten optimiert werden können.
Eignet sich das Lager hinsichtlich Ausrichtung, Struktur und Dimensionierung?
Die Lagerkosten werden maßgeblich durch die Einflussgrößen Lagerstandort, Lagerstruktur und die Dimensionierung beeinflusst. Da eine Änderung dieser Faktoren meist kapitalintensiv ist und viele Abhängigkeiten beispielsweise zwischen Standort und Wohnort des Personals bestehen, scheuen sich viele Lagerverantwortliche jedoch diese Faktoren auf Optimierungspotentiale hin zu überprüfen
Nur bei richtiger Dimensionierung und Struktur des Lagers können Lagerkapazitäten hinsichtlich des Working Capital optimal ausgelastet sein. Viele Unternehmen halten auch aufgrund zu hoher Lagerkapazitäten, zu hohen Lagerbestand vor und sorgen damit für ein zu hohes Working Capital. Gegenteilig kann ein zu kleines Lager dazu führen, dass der Materialfluss und die Lagerlogistik durch die Überauslastung gestört und damit in Ihrer Performance ineffizient werden.
Das Lager muss also passend zur benötigten Lagerkapazität dimensioniert und die Lagerbereiche daraufhin angepasst strukturiert sein. Vor dem Hintergrund, dass ein Lager oftmals mehrere Jahre Bestand haben soll, sich Lagergüter in Typ, Menge und Anzahl verändern können, sind Prognosen über zukünftige Lagerkapazitäten enorm wichtig. Dies bedeutet ebenfalls, dass diese Prognosen im Zuge der Lageroptimierung regelmäßig wiederholt werden sollten, um nicht den Punkt, an dem ein Umzug oder Umbau lohnender als die Weiterbetreibung eines ineffizienten Lagers ist, zu verpassen. Dies ist gelebte Zukunftssicherung!
Ein weiterer Fallstrick ist eine nicht zweckgemäße Auslegung eines Lagers. Ein Lager muss in Zweck, Funktionalität, Standort und den vorgegebenen Anforderungen auf die zu lagernden Güter und die Rolle innerhalb der Supply Chain richtig ausgerichtet sein. Verändern sich Sortiment, Lieferanten oder Absatzmärkte oder gar die Supply Chain, so kann die ehemals richtige Ausrichtung unter den neuen Gegebenheiten kostspielig und ineffizient sein.

Daher sollten Supply Chain Verantwortliche im Rahmen einer Lageroptimierung folgende Bewertung anstellen:
- Veränderung: Haben sich die Gegebenheiten (Lagerzweck, Funktion, Standort, Güterart und -sortiment) im Vergleich zur ursprünglichen Lagerplanung verändert und welche Anforderungen ergeben sich aus den aktuellen Prognosen mittel bis langfristig für das Lager. Dies kann mittels Workshops zur strategischen Lagerausrichtung sowie einer Standortanalyse bewertet werden
- Lagerkapazitäten: Unter der Voraussetzung eines optimalen Lagerbestands je Artikel sowie optimaler Bestellmengen, wie hoch ist die theoretische Auslastung der Lagerkapazität im Vergleich zur tatsächlichen Auslastung. Hierzu eignet sich eine Betrachtung der Lager- und Materialflusskapazitäten im Abgleich zu den tatsächlichen Lagerbewegungen
- Struktur des Lagers: Sind die Anordnung und Dimensionierung der einzelnen Lagerbereiche optimal? In einer Lagerbereichsanalyse kann die Flächenkapazität, Performance und Personalsituation je Lagerbereich geprüft und mit den funktionalen Anforderungen des Lagers abgeglichen werden
- Alternative Lagereinrichtung: Die Produktivität eines Lagers wird durch seine Einrichtung maßgeblich mitbestimmt. Neue Technologie und verschiedene Möglichkeiten schaffen Optionen, um in vorhandenen Strukturen die Produktivität des Lagers zu steigern. Eine Investitions-Bewertung alternativer Regalsysteme, Ladungsbehälter, Fördermittel etc. gibt Aufschluss über Optimierungspotential
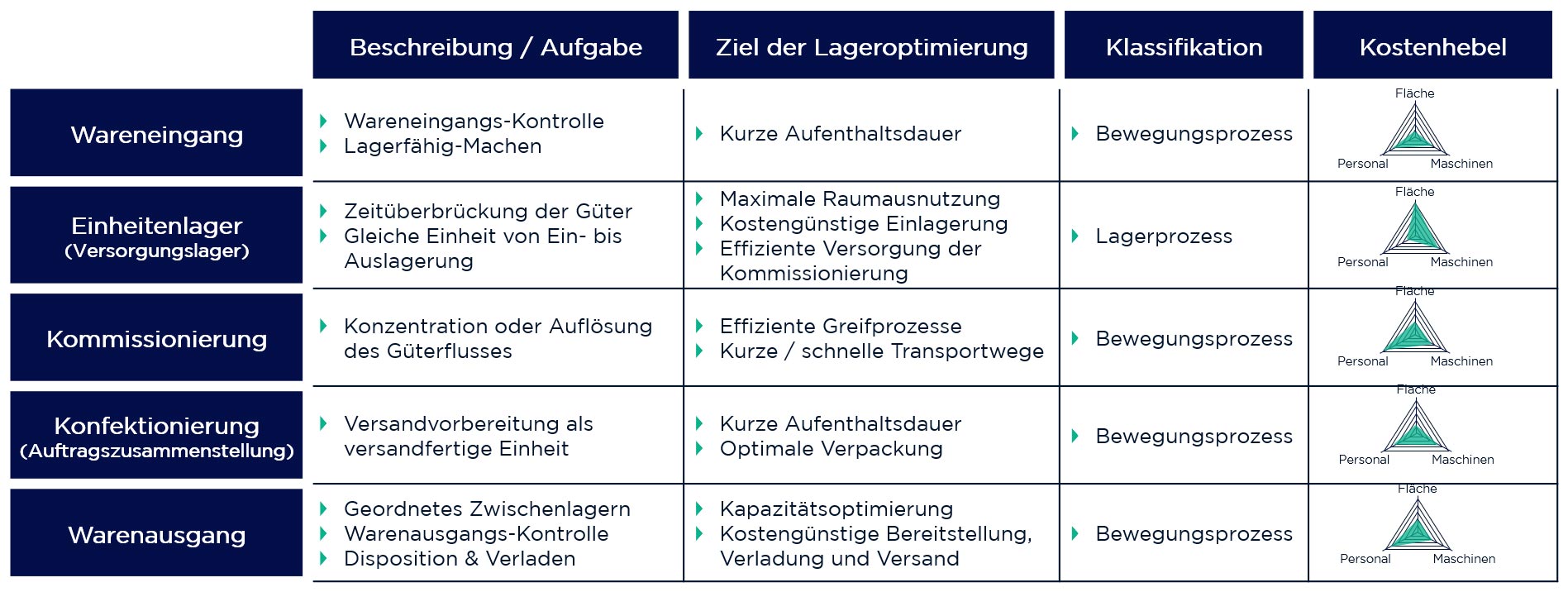
Um eine Entscheidung hinsichtlich des Standortes, der Struktur und Dimension eines Lagers zu treffen, sollte die Verbesserung der Lagerhaltungskosten gesamtheitlich und je Artikel transparent gemacht und gegen die Investitionskosten gerechnet werden. Sollte sich ein Lager weit außerhalb des Optimums befinden, kommen eine neue Lagerplanung, ein Umbau oder Umzug oder die Auslagerung von Artikeln an andere Standorte im Rahmen der Lageroptimierung in Frage.
Wie Sie in der Situation einer Lagerneuplanung auf „grüner Wiese“ vorgehen oder was im Rahmen eines Lagerumbaus zu berücksichtigen ist, können Sie in unserem Artikel zur Lagerplanung erfahren.
Wie kann eine Optimierung der Lagerlogistik und Lagerplatzzuordnung Lagerkosten senken und die Lagerperformance steigern?
Die Lagerlogistik umfasst die Organisation, Steuerung und Durchführung des Materialflusses innerhalb eines Lagers. Der Materialfluss beschreibt den Weg, den ein Gut von Wareneingang bis Warenausgang beschreitet. Hierbei entstehen mit jeder Wegstrecke Transportkosten und mit jeder Zusammenführung und Auftrennung von Artikeln des Materialflusses, zum Beispiel bei der Kommissionierung neue Materialgebinde, die fortan getrennt oder gemeinsam bewegt werden. Da in den meisten Fällen bei der Auslagerung die Aufträge an Artikeln zu- in der Anzahl Einheiten aber abnehmen, entstehen durch diesen Materialfluss höhere Transportkosten bei oftmals höherem Zeitdruck als bei der Einlagerung.
Einfluss auf die durch den Materialfluss verursachten Transportkosten hat neben der Lagerstruktur und den verfügbaren Fördermitteln maßgeblich die Lagerplatzzuordnung oder Lagerorganisation. Insbesondere bei Veränderungen des Artikelsortiments, der Nachfragemengen einzelner Artikel oder neuen Mustern in Auftragszusammenhängen zwischen den Artikeln verändert sich die optimale Lagerplatzzuordnung. Ebenfalls ist die gewählte Lagerplatz Philosophie entscheidend darüber, ob der Materialfluss schnell und kostenoptimal (u.a. Transportwege vs. Working Capital) erfolgen kann.
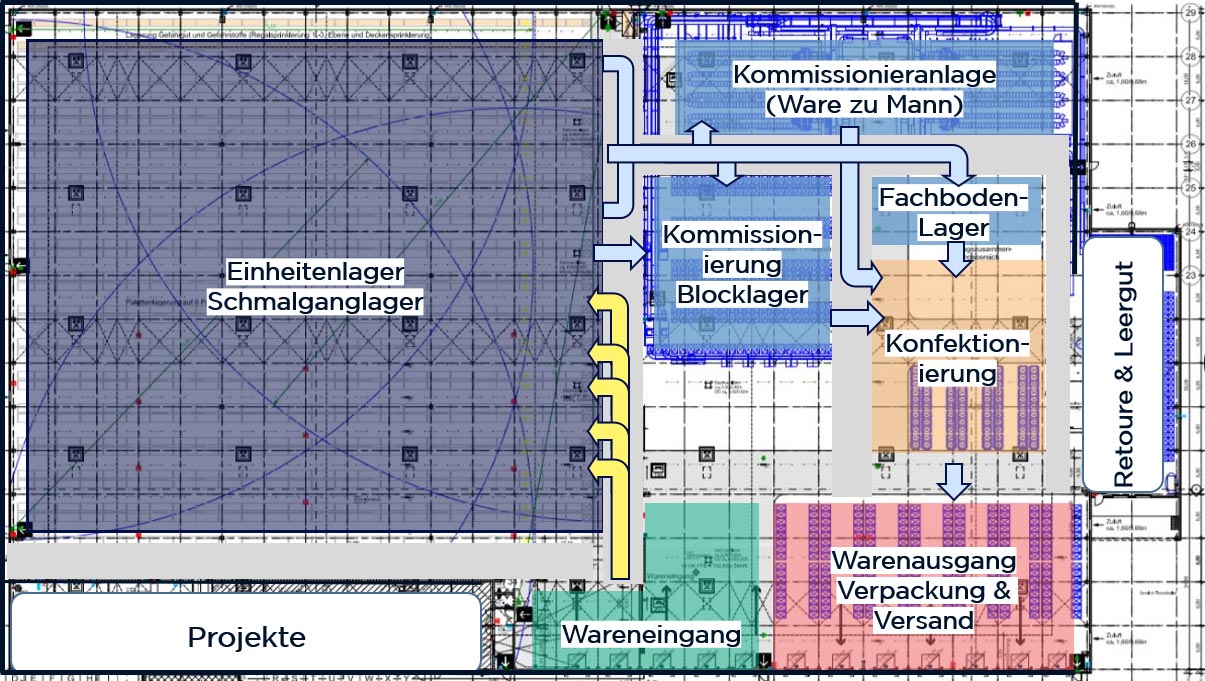
Häufige Auswirkungen ineffizienter Materialflüsse sind lange und damit kostenintensive Transportwege und langsame Durchlaufzeiten. Aus der Erfahrung heraus reagieren viele Unternehmen in solchen Situationen damit, zusätzliches Personal einzusetzen, anstatt den Materialfluss zu bereinigen. Insbesondere in Regallagern oder bei Lagern mit zu wenig Transportflächen kann es sogar dazu kommen, dass ein ungeordneter Materialfluss zu sich gegenseitig blockierenden Förderfahrzeugen führt.
In einem Projektbeispiel zur Lageroptimierung konnten die Lagerhaltungskosten massiv gesenkt werden. Das Lager war überdimensioniert und in seiner Ausrichtung und Nutzung ineffektiv. Die Ressourcenaufwendungen in den Lagerprozessen konnten durch Transportwegeeinsparungen und verbesserte Picking-Leistung (Lagerplatzzuordnung und Verlagerung der Kommissionierarbeiten in die Breitganglager), signifikant gesenkt werden. Darüber hinaus wurden die Flächenkosten des 12.000qm Handelslager um 4.500qm alternativ nutzbare oder vermietbare Flächen gesenkt und das Working Capital durch eine Reduktion der Lagerbestände auf ein Optimum reduziert.

nach der Lageroptimierung
Um den Zustand der Lagerlogistik und des Materialflusses zu prüfen eignet sich die Durchführung einer Materialflussanalyse innerhalb der Lageroptimierung. Diese hilft die Anordnung der Warenlagerbereiche (Lagerlayout) sowie die Transportwege und Fördermittel zu bewerten. Die Analyse hinsichtlich Durchlaufzeiten und Transportkosten und eine entsprechende Darstellung der einzelnen Prozessschritte entlang des Materialflusses kann dabei helfen, Problemfelder zu identifizieren und Verbesserungsmöglichkeiten zu bewerten. Als Verbesserungsmöglichkeiten sollten verschiedene Materialflusskonzepte, alternative Lagerlayouts, eine andere Philosophie der Lagerplatzzuordnung oder eine technische Veränderung der Fördersysteme und Mittel berücksichtigt werden.
Welchen Einfluss haben Kommissioniertechniken, Verpackungssystem und Beladungsplanung
Aufgrund kleinerer Gebindegrößen und höherer Auftragszahlen sind zählen die Kommissionierung, Verpackung und Beladung zu den ressourcen-intensivsten Gebieten eines Lagers und sollten daher auch vor dem Hintergrund einer Lageroptimierung näher betrachtet werden.
Bei der Kommissionierung stellt sich zunächst die Frage nach dem sinnvollen Einsatz eines Kommissionierlagers. Auf Kosten eines zusätzlichen Umlagerungsvorgangs zwischen Einheitenlager und Kommissionierlager sowie zusätzlich benötigter Flächen verkürzt ein Kommissionierlager Transportwege und erleichtert die Greifvorgänge. Darüber hinaus sollte der Einsatz der optimalen Kommissioniertechnik geprüft werden. Je nach Güterart und Umschlagsleistung sowie hierfür bereitstehender Investitions- und Ressourcenkosten ist zwischen einem Ware-zu-Mann und Mann-zu-Ware Kommissioniertechnik zu unterscheiden. Eine Bewertung der Umschlagleistung und den, mit dem Materialfluss verbundenen, Kosten kann Aufschluss darüber geben, ob Mann-zu-Ware Techniken oder deren Weiterentwicklungen wie Pick-by-Light, Pick-by-Voice oder Pick-by-Vision optimal für den Anwendungsfall sind oder eher Ware-zu-Mann Techniken mit vollautomatisch gesteuerten Paletten- oder Behälterregalbediengeräten die Ware zum Kommissionierer bringen. Auf Grund sehr kleiner Bestellmengen, haben diese Erwägungen insbesondere für Fulillment Center eine große Bedeutung.
Im Rahmen der Konfektionierung sollte das Verpackungssystem hinsichtlich effizienter Microprozesse und einer Funktionsüberprüfung der Verpackung geprüft werden. Ablaufprozess-Analysen eigenen sich gut, um Optimierungspotentiale zu identifizieren und praktische Lösungen hierfür zu finden. Oftmals lassen sich in den kleinen manuellen und damit ressourcenintensiven Detailabläufen die relativ gesehen größten Potentiale finden und einfach umsetzen.
Im Rahmen der Beladungsplanung sollten die Versandplanung hinsichtlich einer gleichmäßigen Kapazitätsauslastung untersucht werden. Belastungsspitzen, damit verbundene Wartezeiten und Bereitstellungslagerung führen zu zusätzlich benötigter Lagerfläche und ungleichmäßiger Produktivität der Versandressourcen. Feste Versandslots können über Vereinbarungen oder mithilfe digitaler Slot-Booking Anwendungen vergeben und Optimierungen in diesem Bereich erzielt werden. Ein weiterer Hebel im Rahmen der Beladungskapazitäten ist die Auslastung der Versandkapazitäten. Insbesondere in Branchen mit hoher Kundenmacht oder Wettbewerb in der Lieferzeit sind oftmals freie Versandkapazitäten zu beobachten. Lösungsmöglichkeiten finden sich von kapazitätsorientierten Bestellrabatten, um den Kunden für die Nutzung der Kapazität zu inzentiveren, bis hin zum Einsatz von Frachtenbörsen, um die entstandenen Restkapazitäten anderweitig zu nutzen.
Welchen Beitrag zur Lageroptimierung leistet die Digitalisierung durch ein Warehouse Management System?
Warehouse Management Systeme haben in den vergangenen Jahren die Lagerverwaltung und Lageroptimierung entscheidend vorangebracht. Sie erfassen alle Bewegungen der Lagerlogistik und bilden somit den gesamten Lagerprozesse entlang des Materialfluss über alle Stationen von Wareneingang bis Warenausgang ab. Informationen jedes Prozessschritts können an das Warehouse Management System gemeldet werden.
Zentrale Vorteile eines Warehouse Management Systems sind:
- Unterstützung bei der Working Capital Optimierung der Lagerbestände und Bestellmengen
- Prozessautomatisierung insbesondere bei der Datenerfassung, Kennzahlenberechnung oder Einbindung automatisierter Fördermittel oder Prozessroboter
- Unterstützung bei der Optimierung der Lagerorganisation durch Gruppierung und Sortierung der Artikel im Rahmen der Lagerplatzzuordnung
- Echtzeit Daten und Anschluss an das Unternehmensweite Datensätze (z.B. ERP System) erlauben mittels aktueller Echtzeitwerte auch Prognosen in Entscheidungsfindungsprozessen einzubinden
Im Rahmen einer Lageroptimierung ist bei Bestandssystemen zu prüfen, in wie weit sie die individuell relevanten Vorteile erbringen. Oftmals wird das volle Potential implementierter Systeme nicht genutzt, weil es unzureichend in Prozesse und Entscheidungen angebunden ist oder nicht mit ausreichender Datenqualität und Abdeckung gestützt wird. In vielen Fällen sind vorhandene Systeme auch veraltet und eine Auswahl eines neuen Systems lohnenswert.
Die Anforderungen und Einbindung eines software-gesteuerten Lagers in die Supply Chain sind individuell sehr unterschiedlich und der Anbietermarkt an Softwarelösungen mit über 90 Lösungen unübersichtlich. Somit geraten Auswahl, Implementierung und Weiterentwicklung von Warehouse Management Systemen oftmals zu Mammutprojekten, welche aufgrund mangelnder Erfahrung und Einbindung strategisch relevanter Fragestellungen leider zu oft nicht die gewünschten Ergebnisse bringt.
Lageroptimierung Fazit und Ausblick
Der Wettbewerbsfaktor eines kapazitätsoptimalen Lagers mit niedrigen Lagehaltungskosten, Working Capital sowie schneller Lagerlogistik und hoher Umschlagsleistung kann bei einem hohen Kostenanteil des Lagers immens sein. Die gestiegenen Anforderungen an unsere Logistik und die komplexen, multikausalen Zusammenhänge von Materialfluss, Struktur, Prozessen, Technik und digitalen Möglichkeiten machen die Lageroptimierung zu einer echten, aber sehr lohnenswerten Herausforderung für Ihre Supply Chain Abteilung.
Supply Chain Entscheider und Lagerverantwortliche können dazu beitragen, dass das Lager und die Supply Chain heute und zukünftig bestmöglich aufgestellt ist, indem Sie jetzt für maximale Effizienz und Performance sorgen.
OCM unterstützt Sie bei der Lageroptimierung, Optimierung und Gestaltung Ihrer Lagerlogistik, sowie bei entsprechenden Digitalisierungs-Vorhaben, wie beispielsweise der Auswahl eines geeigneten Warehouse Management Systems. Unser Ziel ist es, gemeinsam mit Ihnen nachhaltige Materialflüsse und Lagerprozesse zu identifizieren, implementieren und evaluieren.
Gerne stellen wir Ihnen unsere Erfahrungen und Projektmodule Supply Chain Consulting & Logistikberatung hierzu vor oder diskutieren anhand Ihrer Herausforderungen konkrete Lösungsansätze.

Unsere Projektmodule im Überblick:
Module Logistik Optimierung & Supply Chain Consulting
Potentialanalyse Logistik & SCM
- Identifikation von Potentialen
- Maßnahmenplan zur Realisierung
Transport Partner Management
- Partnerstrategie und Professionalisierung
- Ressourcensicherung und Schulungskonzept
Ausschreibung Transport
- Professionelle Ausschreibung von Transportdienstleistungen unter Wettbewerb
- Kostenreduzierung Transport
Ausschreibung Fracht- & Logistik
- Kompetitive Bepreisung des exakten Routenprofils
- Qualitäts- und Leistungssicherung
Lageroptimierung & Lagerlogistik
- Kostenoptimierung Warenlager
- Bedarfsgerechtes effizientes Lagerkonzept
Logistik Kooperation
- Transportkosten reduzieren durch Synergie
- Faires und stabiles Kooperationsmodell finden
Tourenplanung & Wegeoptimierung
- Kilometer und Routenreduktion
- Ressourceneinsparung
Supply Chain Netzwerk Design
- Optimierte Kosten je Servicelevel
- Reduzierte Kapitalbindung
Bestands- & Bestellmengen Management
- Bedarfsgerechte Bestand- und Bestellmengenprozesse
- Reduktion Lagerhaltungskosten
Fuhrparkoptimierung
- Optimiertes Fuhrparkkonzept
- Kostenoptimierung & Effizienzsteigerung
Supply Chain & Logistik Strategie
- Ausrichtung der Supply Chain nach Qualität, Verfügbarkeit und Kosten
Digitales Logistikmanagement & Reporting
- Ressourceneffizient
- Aussagekräftige Analysen fundierte Entscheidungen
Interim Manager Logistik & Supply Chain
- Schnelle Hilfe: Kandidaten innerhalb von 48h
- Abgleich von Anforderung und Eignung vom Logistikexperten
- Vom Disponenten bis Logistikleiter