- Supply Chain Strategie
- Supply Chain Netzwerk
- Lagerbestand & Optimale Bestellmenge
- Routenoptimierung
- Ausschreibung Fracht & Distributionslogistik
- Lageroptimierung & Lagerlogistik
- Transportausschreibung
- Digitale Supply Chain

Lagerbestand und Bestellmengen optimieren Working Capital reduzieren
Gut gefüllte Lager, beim Gang durch die Regalreihen ist das ein oder andere verstaubte Regalfach zu beobachten und die Bilanz Position Vorräte ist prall gefüllt. Trotzdem sind immer wieder Artikel nicht dann verfügbar, wenn sie gebraucht werden – wie kann das sein?
Spricht man mit Geschäftsführern und Supply Chain Verantwortlichen über Lagerbestand, Verfügbarkeit und Working Capital, stellt man oftmals fest, das Bestreben, keine unnötigen Bestände anzuhäufen und entweder Working Capital zu reduzieren oder maximale Verfügbarkeit zu erzielen, ist da. Was jedoch offen bleibt ist:
- Finden die Umsetzungsstrategie und die durchgeführten Ansätze die richtige Balance zwischen Verfügbarkeit, OPEX und Working Capital und werden diese effektiv ausgeführt?
- Gibt es Transparenz, Zahlen und Fakten, die belegen, dass das Working Capital optimiert ist, ohne die Verfügbarkeit zum angestrebten Service Level zu beeinträchtigen?
Die Auswirkungen guten Bestandsmanagements auf die OPEX-Kosten, die Verfügbarkeit und das Working Capital können immens sein – frei gewordener Lagerraum kann anderweitig genutzt werden, Lagerprozesse können an Effizienz gewinnen und die Kosten und Kapitalreduktion kann das Unternehmensergebnis verbessern.
- Um Hintergründe und die Situation zu verstehen, betrachten wir die Aufgaben und Funktionen des Bestandsmanagements
- Um Prozesse und das Vorgehen zu überprüfen, beschreiben wir den 3-stufigen Prozess des Bestandsmanagements und geben Hinweise, worauf es zu achten gilt
Mit 2 praktischen Tipps möchten wir auf wichtige Tools und Analysen rund um die Optimierung Ihres Bestandsmanagements hinweisen
Was sind die Funktionen und Aufgaben des Bestandsmanagements?
Bestandsmanagement ist eine der Kerndisziplinen des Supply Chain Managements und hat den Zweck, Ware und Materialen zu bestellen und in der optimalen Menge am richtigen Ort zum richtigen Zeitpunkt für den Bedarfsfall bereitzustellen. Durch die zeitliche und mengenmäßige Differenz von eingehenden und ausgehenden Materialflüssen eines Lagers erfüllen sie sozusagen eine Pufferfunktion.
Welche konkreten Funktionen erfüllt der Lagerbestand? Es gibt 5 wesentliche Funktionen, die je nach Unternehmen und Ausrichtung des Lagers zum Tragen kommen:
- Größendegressions- oder Stückkosteneffekt: Dieser entsteht, wenn beim Einkauf, Transport oder in der Produktion durch Abnahme oder Verwendung von höheren Bedarfsmengen die Stückkosten reduziert werden können (Bspw. Mengenrabatte, Auslastung von Transportkapazitäten, Rüstkostenreduktion bei Erhöhung der Produktionslosgrößen, etc.)
- Angebots-Nachfrage-Überbrückung: Weichen Angebot und Nachfrage, beispielsweise aufgrund von Saisonalität oder anderen Zyklen voneinander ab, so dient der Lagerbestand der zeitlichen Überbrückung des Angebots mit der Nachfrage
- Prozessbeschleunigung: Wenn im Absatzmarkt oder der Produktion keine mit der Artikelverwendung synchronisierte Bereitstellung erfolgen kann, so helfen Lagerbestände dabei die Nachfrage schnell zu decken
- Spekulation im Fall von erwarteten Preisanstiegen oder niedrigen Absatzpreisen
- Schutz vor Unsicherheit, wenn der Materialzufluss oder Materialabfluss anders als erwartet verlaufen
Da diese Funktionen zwar insbesondere zur Prozesseffizienz oder der Preisabsicherung dienen, verursacht Lagerhaltung aber auch Kosten: Neben Lagerraum-, -Personalkosten sowie den Opportunitätskosten des gebundenen Kapitals (Working Capital) birgt die Lagerung zusätzlich Risiken durch Wertveränderungen oder ausbleibende Nachfrage. Die Optimierung dieser Kosten und Risiken ist eine weitere Aufgabe und Funktion des Bestandsmanagements.
Somit stehen die Kosten und Risiken des Lagerbestands stets in Abwägung mit den im Zufluss und Abfluss generierten oder verhinderten Kosten. Dieser Zielkonflikt stellt ein klassisches Optimierungsproblem dar, welches das Bestandsmanagement versucht zu lösen.

Viele Unternehmen beantworten die Frage der Zielausrichtung des Bestandsmanagements oder der Bestandsdisposition mit einer angestrebten Reduzierung von Lagerbeständen unter der Voraussetzung, die Verfügbarkeit zum vereinbarten Service Level und die damit verbundene Kundenzufriedenheit mindestens beizubehalten. Je nach Unternehmenssituation, Supply Chain Strategie und höheren Unternehmensstrategie ist ein anderes Zielsystem sinnvoll und sollte im Rahmen der Supply Chain Strategie festgelegt werden.
Um diese Aufgaben zu erfüllen, folgt man im operativen Bestandsmanagement einem 3-stufigen Prozess: die Bedarfsermittlung, die Lagerbestandsplanung und die Beschaffungsplanung.
Um das Bestandsmanagement entlang von Zielvorgaben auszurichten oder ein Bestandssystem zu bewerten und zu optimieren, benötigt es der Vorgabe eines Zielsystems. Das formulierte Zielsystem beeinflusst die Lieferfähigkeit und die Kosten des Unternehmens, weshalb es im Rahmen der Supply Chain Strategie gemeinsam mit dem Unternehmensmanagement erarbeitet und festgelegt werden sollte.
Grundsätzlich unterscheidet man drei Dimensionen, die in einem Zielsystem beschrieben werden sollten:
- Verfügbarkeit und Service Level legen die mengen-, termin- und qualitätsmäßige Sicherstellung der Lieferfähigkeit fest
- Vorgaben zum internen Kapitalkostensatz und daraus resultierende Working Capital oder Kapitalbindung begrenzen die Mittel, welche zur Bevorratung der Güter, Materialien und Produkte zur Verfügung gestellt werden
- Mit den Lagerbestandskosten werden die Kosten beschrieben, welche kontinuierlich im Rahmen der Lagerung anfallen (Lagermiete, Personalkosten, Bestellkosten etc.)
Um ein Zielsystem zu beschreiben und festzulegen, sind verschiedenen Situationen und Szenarien zu unterscheiden und zu berücksichtigen:
- Bewertet man ein Lager oder die Gesamtheit aller Lager?
- Handelt es sich um eine einstufige oder mehrstufige Lagerstruktur (z.B. Zentrallager, das lokale Lager beliefert)?
- Was für einen Zweck erfüllt das Lager (Dispositionslager, Produktionslager, Vendor-Managed-Inventory etc.)?
- Welche Supply Chain beziehungsweise Produktions- und Steuerungskonzepte verfolgt das Unternehmen (Push vs. Pull-Prinzip (Kanban, Just-in-time)?
Die unterschiedliche Ausgangslage ist unbedingt in der Ausrichtung des Bestandsmanagements, wie auch bei dessen Bewertung zu berücksichtigen.
Um die vorgegebene Ausrichtung in der Operative sicherzustellen, empfehlen wir die Ausarbeitung relevanter Lagerkennziffern und KPIs. Diese sollten gemeinsam mit der Zielausrichtung für das Bestandsmanagement vorgegeben werden. Es gibt zahlreiche Lagerkennziffern zu den häufigsten gehören: durchschnittlicher Lagerbestand, Wareneinsatz, Umschlagshäufigkeit, durchschnittliche Lagerdauer, Lagerzinssatz, Bestands- und Lagerreichweite und der Lagerkostensatz.
Wie sieht der 3-stufige Bestandsmanagement Prozess aus – worauf ist zu achten?
Der optimale Lagerbestand eines Artikels hängt wie beschrieben von der verfügbaren Lagerfläche, dem Zeitpunkt und der benötigten Menge des Bedarfs, der vorgelagerten Beschaffungsverfügbarkeit und -dauer sowie den verursachten Kosten ab. Um die gesetzten Ziele hinsichtlich Lieferfähigkeit und Kosten unter diesen Bedingungen zu erreichen, müssen Entscheidungen zum optimalen Lagerbestand, der Bestellmenge und des Bestellzeitpunktes getroffen werden.
Der 3-stufige Bestandsmanagement Prozess beschreibt, wie diese Entscheidungen getroffen werden können, worauf es zu achten gilt und wie die Schritte sich für unterschiedliche Artikel unterscheiden sollten.
Schritt 1: Bedarfsermittlung / Dispositionsverfahren - Wann muss wieviel vorrätig sein?
In der Bedarfsplanung versucht man die Frage zu beantworten, wann in der Zukunft welcher Bedarf für einen bestimmten Artikel eintritt. Hierbei unterscheidet man zwischen 3 prinzipiellen Ausgangssituationen und zugleich 3 unterschiedlichen Arten an Dispositionsverfahren oder Methoden der Bedarfsermittlung.

A) Auftragsgesteuerte Disposition:
Hierbei erfolgt die Bestellung des benötigten Artikels erst im Zeitpunkt des erhaltenen Auftrags. Voraussetzung ist eine rechtzeitige Lieferzeit und Lieferverfügbarkeit des Artikels, um die zeitlichen und mengenmäßigen Anforderungen des Auftrags einhalten zu können. Je nach Ausgestaltung ist diese Art der Disposition personalintensiv, weshalb sie meist nur für Artikel mit hohen Lagerhaltungskosten oder sehr unregelmäßigem Bedarf genutzt wird. Diese Methode der Bedarfsermittlung zeichnet sich dadurch aus, dass Lagerhaltung, aus dem Gesichtspunkt der Artikellieferfähigkeit, nahezu vermieden werden kann und keine Prognose über den Zeitpunkt und die Menge des Bedarfs benötigt wird. Im Schiffbau, im Fahrzeugbau, spezielleren Medikamenten, Impfungen oder angefertigten Brillen befinden sich die meisten benötigten Artikel nicht auf Lager und werden erst bei Auftrag beschafft.
B) Programmgesteuerte / Deterministische Disposition:
Bei programmgebundenen oder definitiv-bestimmbaren (deterministischen) Bedarfen, ist der Primärbedarf an Produkten in Menge und benötigtem Zeitpunkt am Lieferpunkt bekannt. Man spricht auch von einem abhängigen oder koordinierten System, da der Sekundärbedarf an vorgelagerten Artikeln vom Primärbedarf abgeleitet werden kann.
Diese Situation ist beispielsweise bei Produkten, die nach einem vorgegebenen Produktionsplan produziert werden (Material Requirements Planning) oder die in konkreten Kundenaufträgen (Distributions Requirements Planning) benötigt werden, gegeben. Der Sekundärbedarf an vorgelagerten Artikeln kann dann entsprechend definierter Stücklisten systemisch errechnet werden. Dieses Verfahren ist dann geeignet, wenn die Vorausplanung ausreichend Zeit zur Beschaffung lässt, Stück- und Artikelbedarfslisten sauber gepflegt sind und die oftmals sehr rechenintensive Bestimmung systemisch übernommen werden kann.
Ein Beispiel für programmgesteuerte Bedarfsermittlung findet sich in der Pharmaproduktion oder der Lebensmittel Industrie. Produktionsanlagen können hier häufig mehrere Artikelsorten herstellen und die Produktionsprogramme sind oft Wochen im Voraus geplant. Durch die geplante Produktionsmenge und die bekannte Rezeptur können die erforderlichen Mengen an Inhaltsstoffen im Voraus bestimmt werden.
C) Verbrauchsgesteuerte Disposition:
Handelt es sich um Artikelbedarfe, die nicht deterministisch bestimmbar sind und deren Bestellung nicht erst im Auftragszeitpunkt erfolgen kann, so ist der zukünftige Bedarf aus dem Betrachtungszeitpunkt heraus in Menge und Zeitpunkt ungewiss (man spricht auch von unabhängigen Systemen). Zur Ermittlung des zukünftigen Bedarfs muss demzufolge eine Prognose erstellt werden. Neben der subjektiven Schätzung, die meist auf Meinung über einen mutmaßlichen Bedarf der Zukunft rein intuitiv vorgenommen wird, existieren hierzu verschiedene stochastische Prognoseverfahren. Stochastische Prognoseverfahren nutzen i.d.R. Vergangenheitsdaten oder Absatzprognosen, um den zukünftigen Bedarf zu schätzen.
Die stochastische Prognose muss nicht zwingend besser sein als eine Intuitivschätzung. Je schwankender und unregelmäßiger ein Bedarf ist, desto schwieriger fällt die Prognose allgemein. Prognosefehler haben eine Entnahmeüberziehungen oder eine Wiederbeschaffungszeitüberziehung für den Lagerbestand zur Folge. Vor dem Einsatz eines stochastischen Verfahrens, sollte stets geprüft werden, ob die Voraussetzung für den sinnvollen Einsatz stochastischer Verfahren gegeben sind. Diese sind nur dann sinnvoll einzusetzen, wenn die Vergangenheitswerte ausreichend und zuverlässig genug sind und die Zeitstabilitätshypothese Gültigkeit besitzt. Die beste Vorgehensweise besteht meist aus einer Kombination der Prognoseverfahren und der Möglichkeit, diese mit nicht-historischen Informationen, beispielsweise aus anderen Datenquellen oder von Bedarfplanern, zu ergänzen oder zu überstimmen. Häufige Methoden der stochastischen Prognose sind die Mittelwertbildung, Methoden der exponentiellen Glättung und die Regressionsanalyse.
Während die deterministische Bedarfsermittlung vorwiegend bei hochwertigen und Artikeln mit hohen Lagerhaltungskosten eingesetzt wird, verwendet man bei geringwertigen gängigen Artikeln sowie bei den Hilfsstoffen und Betriebsstoffen (Tertiärbedarf) oftmals die stochastische Bedarfsermittlung.
Ein sehr bekanntes Beispiel ist die Modeindustrie, in der die Produktion weit vor der Verkaufssaison die Produkte herstellt. Ein weiteres Beispiel ist der Bedarf an Standardschrauben oder Standard-Ersatzteilen in Produktionsstätten des produzierenden Gewerbes.
Schritt 2: Lagerbestandsplanung – Wieviel Bestand deckt den Bedarf?
Im Anschluss an die Ermittlung des Bedarfs, folgt die Bestandsplanung. Hier gilt es festzulegen, wie sich der Lagerbestand über die Zeit verhalten sollte, um die zukünftigen Bedarfe erfüllen zu können, ohne limitierende Lagerrestriktionen zu reißen. In anderen Worten werden in der Bestandsplanung Lagerbestandsgrenzen festgelegt, innerhalb derer sich der Bestand bewegen sollte.
Die relevantesten Lagerbestände sind:
- Der Sicherheitsbestand, welcher zu einer festgelegten Wahrscheinlichkeit selbst unter Schwankungen die Lieferfähigkeit garantiert
- Der Bestellauslösebestand, welche die Nachfrage- und Zulieferprozesse berücksichtigt gibt den Bestellzeitpunkt vor, um die Zeitdauer bis zum Erhalt einer Bestellung abzudecken
- Der Maximalbestand, der unter Wahrung der Lagerestriktionen gerade noch eingelagert werden kann
- Der durchschnittliche Lagerbestand, welcher zur Berechnung des Working Capital verwendet wird
Die Bestandsplanung ermittelt den optimalen Sicherheitsbestands sowie den Bestellzeitpunkt bzw. den Bestellauslösebestand unter Berücksichtigung stochastischer oder deterministischer Nachfrage- und Zulieferprozesse.
- Wieviel Bestand sollte als Sicherheitsbestand auf Lager liegen?
- Wann soll zur Wiederauffüllung des Lagerbestandes bestellt werden?
Je nachdem, ob sich Nachfrage und Zulieferung deterministisch oder stochastisch verhalten, gibt es verschiedene Ansätze zur heuristischen oder exakten Berechnung der Bestände. In der Praxis ist es wichtig zu prüfen, ob die Voraussetzungen der jeweiligen Methode erfüllt sind, oftmals liefern Heuristiken wesentlich einfacherer zu bestimmende und ausreichend gute Antworten.
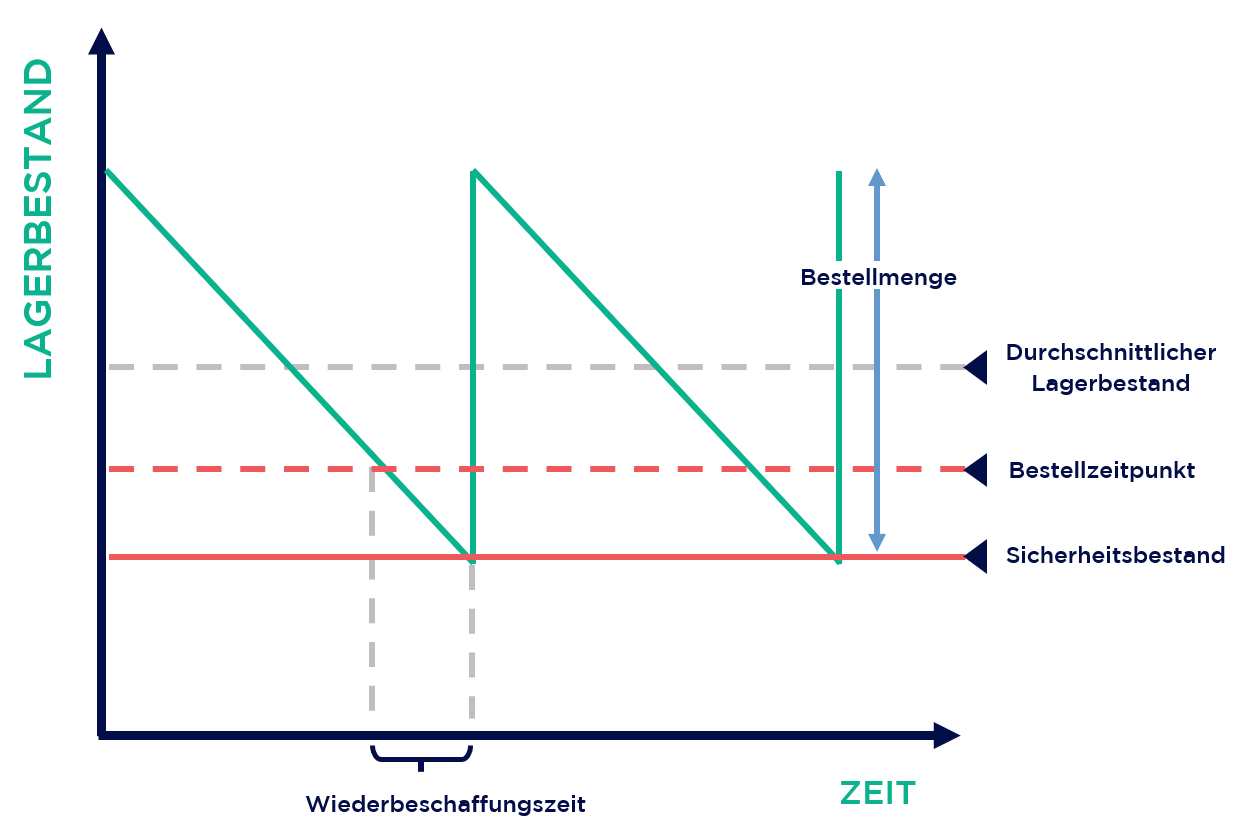
Schritt 3: Beschaffungsplanung – wie muss ich bestellen, um den angestrebten Bestand zu erhalten?
In der Beschaffungsplanung wird anschließend die Bestellpolitik festgelegt, welche den Bestellzeitpunkt und die Bestellmenge mit Hilfe passender Verfahren artikelindividuell ermittelt. Um die im Zusammenhang bestehenden Kosten (Bestellkosten, Bestellmengenrabatte, Lagerhaltungskosten, Wertverfallkosten, etc.) zu berücksichtigen, eignen sich optimierende Losgrößenverfahren, welche Bedarfsmengen mehrerer Perioden kostenoptimal zu Losgrößen zusammenfassen. Auch hier gibt es wieder verschiedene Politiken, Heuristiken und Modelle zur Ermittlung – die Wahl einer geeigneten Methode sollte im Einzelfall geprüft und getätigt werden.
Die Beschaffungsplanung / Beschaffungspolitik beantwortet:
- Wie viel soll zur Wiederauffüllung des Lagerbestandes bestellt werden?
- Wie oft soll bestellt werden?

Die Optimierung des Bestandsmanagements kann erhebliche Kosteneinsparungen generieren, jedoch ergibt sich aus der Verpflichtung zur Lieferfähigkeit und der sich schnell ergebenen Komplexität bei ausreichend großer Artikelvielfalt schnell eine große Herausforderung für die Logistikabteilungen.
Da die Verfahren unterschiedlich aufwendig und geeignet sind, ist daher eine der wichtigsten Entscheidungen, für welche Artikel welche Art des Bestandsmanagement erfolgen soll und welche Artikel überhaupt auf Lager liegen.
Tipp 1: Ist der Artikel Teil des Sortiments & welche Art von Bestandsmanagement ist sinnvoll?
Ist es sinnvoll alle Artikel und Güter zu lagern und wenn ja, wie sollen die Bestände gemanagt werden? Wirtschaftlich gesehen, sollte ein Gut nur dann gelagert werden, wenn die Kosten der Fehlmengen infolge einer Nichtlagerung größer sind als die mit der Lagerung verbundenen Kosten.
Wichtigkeit:
Es geht zum einen um die Höhe der Fehlmengenkosten eines Artikels. Die Fehlmengenkosten können Wartezeiten oder Umsatzausfälle bedeuten. Insbesondere sollten darüber hinaus auch Verbundeffekte berücksichtigt werden. Die Folgen eines fehlenden Artikels im Supermarkt, wenn es Alternativartikel gibt, sind wahrscheinlich deutlich geringer, als wenn eine günstige Schraube, die aber unbedingt für die Fertigstellung eines Fahrzeugs benötigt wird, dessen Verkauf verhindert.
Beschreibt man den kumulierten Wertanteil der Artikel in aufsteigender Reihenfolge (Lorenzkurve) wie im 80-20 Prinzip, so lässt sich im Vergleich verschiedener Lager und Branchen beobachten, dass in Lagern, die näher auf den Endverbraucher ausgerichtet sind, die Wertkonzentration auf mehr Artikel verteilt ist und die Kurve etwas abflacht.
Planbarkeit und Häufigkeit:
Zum anderen geht es in der zeitlichen Dimension darum, wie die Verbrauchsstruktur des Artikels aussieht. Bei regelmäßigem Verbrauch kann eine einsatzsynchrone Anlieferung die Lagerdauer reduzieren oder ganz vermeiden. Bei schwankendem und unregelmäßigem Verbrauch würde das Vorhalten eines Artikels dazu führen, dass Mengen sehr lange lagern und bei einer hohen Schwankungsbreite auch erhebliche Mengen vorgehalten werden müssten.
Ansatz der selektiven Lagerhaltung:
Mit dem Ansatz der selektiven Lagerhaltung kann man beide Dimensionen berücksichtigen und so entscheiden, welche Teile des Sortiments gelagert werden sollen und wie das Bestandsmanagement für diese Teile aussehen soll.
Das Anfertigen einer Artikelwert-, Artikelumsatzstatistik oder des Artikel-Gewinn Beitrags ermöglicht es, die Artikel zu bestimmen, die von hoher Wichtigkeit für das Unternehmen sind.
Um mögliche Verbundkosten oder Zusammenhänge mit anderen Artikeln zu berücksichtigen, ist es insbesondere in Produktionslagern sinnvoll die Bewertung durch den kritischen Wert eines Artikels zu ergänzen.
Für verbrauchsgesteuerte Artikel lässt sich die Planbarkeit aus einer Analyse der historischen Artikelverbräuche und deren Nachfrage-Muster bestimmen.

Die Entscheidung über die Lagerung eines Gutes wird außerdem wesentlich von seiner Verbrauchsstruktur abhängen. So bieten sich bei einem regelmäßigen Verbrauch die einsatzsynchrone Anlieferung, bei einem schwankenden Verbrauch die Lagerung und bei einem unregelmäßigen Verbrauch die Einzelbeschaffung im Bedarfsfall an.
Die Anwendung des ABC-Prinzips führt dazu, dass die A-, B- und C-Artikel im gesamten Bereich der Lagerhaltung oder in bestimmten Teilbereichen unterschiedlich behandelt werden. So kann für jede Artikelklasse der Bestellvorgang anders ablaufen, die Lieferbereitschaft unterschiedlich hoch sein und die Anzahl der Auslieferungspunkte verschieden sein. Wenn man z. B. in einem Unternehmen vor Einführung der selektiven Lagerhaltung alle Artikel in einem Bestellzyklus von acht Wochen bestellt hat, kann man nach Durchführung einer ABC-Analyse mit verschiedenen Bestellzyklen arbeiten.
Eine sinnvolle Aufteilung kann beispielsweise sein:
- A/X: Planbare und wichtige Artikel können beispielsweise in Just-in-Time Supply Chains abgewickelt werden oder mit auftragsbezogenen Bestandsverfahren mit ausreichender Überwachung so betreut werden
- C/X Planbare und weniger wichtige Artikel können durch die verbrauchsgesteuerten Bestellmanagementverfahren ausreichend sicher und günstig im Verfahren betreut werden. Die Lagerung sollte eher zentral an wenigen Punkten des Netzwerks stattfinden
- A/Z Wenig planbare aber wichtige Artikel sollten in ausreichender Menge gelagert sein und hier bieten Möglichkeiten wie Konsignationslager oder customer-managed-inventories eine gute Alternative, um die Lieferfähigkeit zu garantieren und die Kosten gegebenenfalls gering zu halten. Generell erfolgt die Lagerung lokaler als bei C/X Artikeln
- Wenig planbare und unwichtige Artikel sollten in den meisten Fällen nicht als Lagerartikel im Sortiment vorliegen oder wenn doch, dann ausschließlich in einem Zentrallager bevorratet sein
TIPP 2: Wie kann die Leistung des Bestandsmanagements bewertet werden?
Im Folgenden geben wir Einblick in einige Methoden, um die Leistung des Bestandsmanagements in den wesentlichen Dimensionen Lieferfähigkeit, Kosten und Performance zu bewerten.
Probleme in der Lieferfähigkeit:
- Die Analyse von Stock-Out über die Zeit sowie die Mengen- und Termintreue entlang vorgegebener α- oder β- Service Leveln geben Aufschluss darüber, in wie weit ein Lager von den strategischen Vorgaben abweicht.
- Analyse der dokumentierten Ausnahme-Bestellungen (Übersteuerung Bestellvorschläge, Unterschreitung der Sicherheitsbestände, Sondermeldungen)
Bestandslevel - Reichweitenanalyse / Lagerumschlags-Analyse:
- Eine Bewertung der tatsächlichen Bestände kann beispielsweise mit einer Reichweitenanalyse oder Lagerumschlagsanalyse, welche die Lagerbestände mit den aktuellen Abverkäufen / Umschlägen ins Verhältnis setzt, erfolgen
Sortiment und Dispositionsverfahren:
- Eine ABC/XYZ Analyse und ein Vergleich der Lieferfähigkeit und Bestandslevel innerhalb der Artikelklassen, um Abweichungen und eine Einhaltung vom Sortimentsgedanken zu überprüfen. Überprüfung der Melde- und Sicherheitsbestände, sowie verwendeten Heuristiken und Prognosen, um Fehler in der Bedarfsermittlung und Bestandsfestsetzung zu überprüfen.
Systemabgleich:
- Ein Abgleich der ABC/XYZ Analyse mit der entsprechenden Klassifizierung in SAP, um die Aktualität der Daten zu überprüfen
- Analyse der in den Artikelstammdaten hinterlegten Parameter (Dispositionsverfahren, Melde- & Sicherheitsbestände, Plandaten, …)
Benchmarking der oben genannten Kriterien auf Lagerebene innerhalb der gleichen Supply Chain Stufe oder von Artikeln innerhalb eines Lagers in Verbindung mit Interviews mit den involvierten Logistikern ermöglicht in der Regel schnell die Pain Points zu identifizieren und gemeinsam geeignete Maßnahmen zur Verbesserung zu entwickeln.
Fazit und Rolle der Digitalisierung
Durch weiter wachsende Kundenanforderungen hinsichtlich Lieferfähigkeit und zunehmender Spezialisierung entlang der Supply Chain wachsen die Herausforderungen an das Bestandsmanagement zunehmend.
Durch den Einsatz von Technologie und permanenter Datenerfassung gelingt es Unternehmen auch die komplexesten Supply Chains optimal zu managen und sich so einen Wettbewerbsvorteil zu erarbeiten. Die Nutzung dieser Technologien ist die Basis - die Zukunft wird sich durch zunehmende vertikale und horizontale Integration angrenzender Systeme entscheiden. Vertikal werden vom Zulieferer bis zum Endkunden alle Artikelbewegungen und Bestände entlang der Supply Chain Schritte bekannt sein und horizontal werden Einkauf, Vertrieb-, Marketing und andere Funktionen in ihren Aktionen und Reaktionen mit in ein optimales Bestandsmanagement eingebunden sein.
Basis für diese Entwicklungen sind neben soliden Daten jedoch vor allem funktionierende Methoden und Prozesse im Rahmen des Bestandsmanagements. Um Working Capital zu optimieren und Kosten zu senken, sollten Unternehmen heute in eine passende strategische Ausrichtung, transparente Leistungsmessung und klare Bestandsmanagement Prozesse investieren.
Eine einfache und doch sehr effektive Methode ist das Konzept der Economic Order Quantity, dessen Wirkung nicht unterschätzt werden sollte. Wenn man es mit relevanten Informationen und sinnvollen Erweiterungen, wie Rundungsregeln etc., versieht, stellt das EOQ-Konzept ein leistungsstarkes Werkzeug dar, um die optimale Balance zwischen Verfügbarkeit, Kapitalkosten und OPEX zu gewährleisten.
Wir helfen Ihnen bei der Optimierung und Gestaltung Ihres Bestandsmanagements, der Ausgestaltung Ihres Supply Chain Netzwerks oder Lagers sowie entsprechenden Digitalisierungs-Vorhaben.
Gerne stellen wir Ihnen unsere Erfahrungen und Projektmodule Supply Chain Consulting & Logistikberatung hierzu vor oder diskutieren anhand Ihrer Herausforderungen konkrete Lösungsansätze.

Unsere Projektmodule im Überblick:
Module Logistik Optimierung & Supply Chain Consulting
Potentialanalyse Logistik & SCM
- Identifikation von Potentialen
- Maßnahmenplan zur Realisierung
Transport Partner Management
- Partnerstrategie und Professionalisierung
- Ressourcensicherung und Schulungskonzept
Ausschreibung Transport
- Professionelle Ausschreibung von Transportdienstleistungen unter Wettbewerb
- Kostenreduzierung Transport
Ausschreibung Fracht- & Logistik
- Kompetitive Bepreisung des exakten Routenprofils
- Qualitäts- und Leistungssicherung
Lageroptimierung & Lagerlogistik
- Kostenoptimierung Warenlager
- Bedarfsgerechtes effizientes Lagerkonzept
Logistik Kooperation
- Transportkosten reduzieren durch Synergie
- Faires und stabiles Kooperationsmodell finden
Tourenplanung & Wegeoptimierung
- Kilometer und Routenreduktion
- Ressourceneinsparung
Supply Chain Netzwerk Design
- Optimierte Kosten je Servicelevel
- Reduzierte Kapitalbindung
Bestands- & Bestellmengen Management
- Bedarfsgerechte Bestand- und Bestellmengenprozesse
- Reduktion Lagerhaltungskosten
Fuhrparkoptimierung
- Optimiertes Fuhrparkkonzept
- Kostenoptimierung & Effizienzsteigerung
Supply Chain & Logistik Strategie
- Ausrichtung der Supply Chain nach Qualität, Verfügbarkeit und Kosten
Digitales Logistikmanagement & Reporting
- Ressourceneffizient
- Aussagekräftige Analysen fundierte Entscheidungen
Interim Manager Logistik & Supply Chain
- Schnelle Hilfe: Kandidaten innerhalb von 48h
- Abgleich von Anforderung und Eignung vom Logistikexperten
- Vom Disponenten bis Logistikleiter